Revolutionizing Manufacturing: The Outlook of Injection Molding Advancements
A realm of manufacturing is on the verge of a transformative change, with innovations in injection-molding technologies leading the charge. As sectors strive for greater productivity, sustainability, and excellence, the demand for sophisticated injection molder technologies is becoming increasingly pronounced. This process, which has been a foundation of production for decades, is being improved by cutting-edge developments that offer the potential to transform how goods are manufactured.
From smart automation systems to the integration of AI, the prospects of injection molding is promising with opportunities. Manufacturers are now able to produce intricate designs with unmatched precision and efficiency, greatly minimizing waste and energy consumption. As we examine the newest advancements in this industry, it becomes the progress of this process holds the capacity to transform not only production lines but also the wider field of industrial manufacturing.
Advancements in Material Science
The field of injected molding is experiencing substantial transformations in the science of materials, resulting in improved properties and uses. Traditional materials like plastic composites are continuously enhanced with innovative polymers that offer higher strength, reduced weight, and better thermal stability. These developments allow producers to create more durable and versatile products, fulfilling the increasing demands of different industries, ranging from car manufacturing to consumer electronics.
Plant-based and recyclable materials are also growing in traction, showing a trend towards more sustainable manufacturing practices. The creation of biodegradable plastics and composites can minimize the environmental footprint of molded products. This movement not only conforms with global sustainability goals but also attracts to eco-conscious consumers, prompting sectors to consider more sustainable options in their production processes.
Moreover, intelligent materials embedded with sensors are being developed, enabling injection molded parts to monitor and respond to their environments. These materials can offer immediate data feedback, improving performance and reliability in critical applications. As these advancements continue, the possibility for customized solutions in injection molding grows, opening up opportunities for new designs and functionalities in the future.
Automation and Intelligent Systems
The emergence of automated solutions and smart technology is transforming the landscape of injection moulding. Advanced robotics are being incorporated into manufacturing processes, allowing for increased precision and speed. With robotic systems handling mundane chores, manufacturers can cut labor costs and mitigate the risk of human error. This technology not only streamlines production but also enhances product consistency, which is a critical factor in upholding quality standards.
Additionally, smart technology is paving the way for data-informed decision-making in injection molding processes. Devices equipped with monitoring systems monitor various parameters in real-time, allowing operators to examine performance metrics and identify potential issues before they worsen. Proactive maintenance, powered by AI algorithms, helps in reducing downtime by anticipating breakdowns, thus guaranteeing a smooth production workflow. This transition towards smart manufacturing is setting new standards in production efficiency.
Furthermore, the integration of IoT capabilities allows for enhanced connectivity among different production units. Molders can now monitor and manage their operations remotely, obtaining insights into their equipment and workflow efficiency. This degree of connectivity not only enhances productivity but also promotes sustainable practices by maximizing resource utilization. As these technologies continue to evolve, the injection molding industry is set for remarkable growth and innovation.
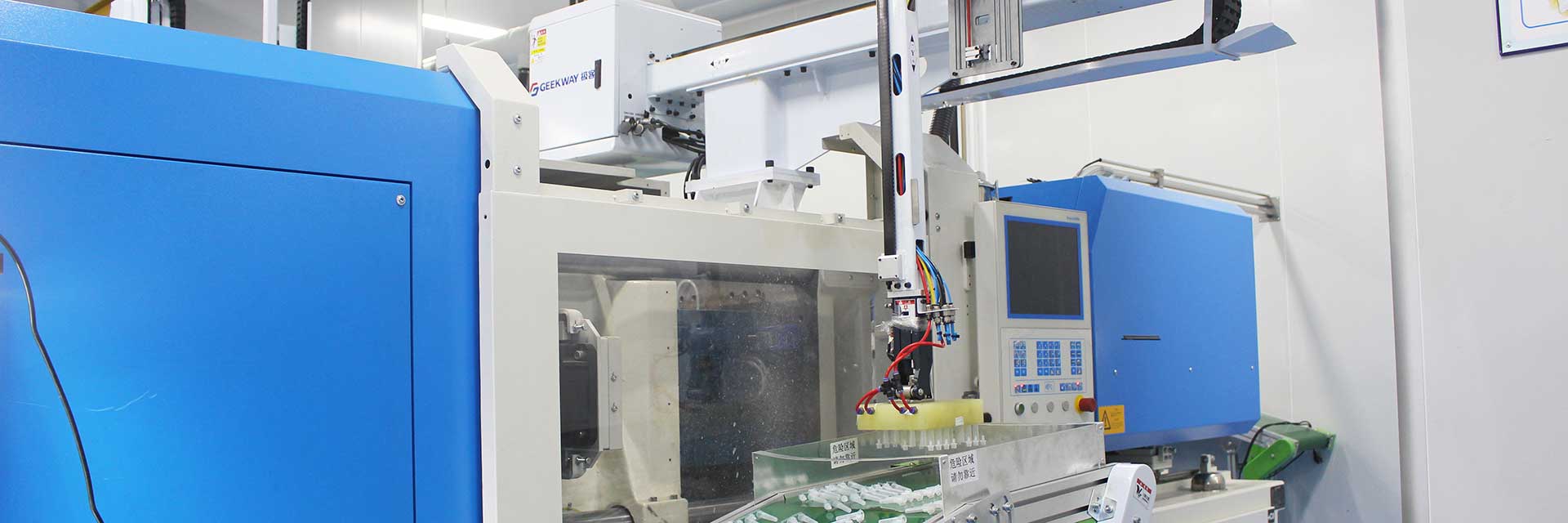
Eco-friendliness in Injection Molding
Sustainability in injection molding is a major focus as businesses aim to reduce their impact on the environment. The sector is experiencing a move towards more sustainable practices, including the application of recyclable materials and the creation of bioplastics. These advancements not only boost the environmental responsibility of products but also allow manufacturers to fulfill the increasing demand for environmentally responsible solutions from the market.
Efficient energy use is another key focus area in green injection molding. Advancements in technology have led to the development of highly efficient injection molders that use less energy while preserving rapid production rates. Companies are also turning to alternative energy sources, such as solar power and wind energy, for their work. This adoption with clean energy sources greatly decreases the greenhouse gas emissions associated with the production process.
Moreover, closed-loop systems are being used to minimize scrap in mold manufacturing. By repurposing scrap resources and optimizing production processes, manufacturers can greatly cut waste generation. This method not only contributes to a circular economy but also helps businesses reduce on costs. As the sector continues to evolve, the dedication to sustainability will be vital in shaping the future of mold manufacturing.